As the shirts whiz by ...
By Laura Collins
Published in News on June 1, 2010 1:46 PM

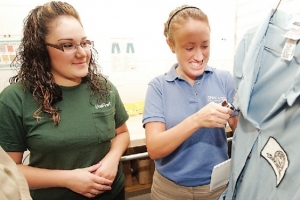
Troy Herring
UniFirst employee Isela Castaneda observes and instructs News-Argus reporter Laura Collins on how to remove name and business patches from old used uniforms. During her day long stint as a UniFirst employee, Ms. Collins helped hang, steam and organize uniforms.
The Job: Steamer, sorter
The Company: UniFirst Corporation
The Location: Goldsboro
Dear Ricky,
Sorry about your shirt.
Sincerely,
Laura
"That'll be $20," said UniFirst plant manager John Gedeon after I ripped a hole in a shirt while trying to remove a patch. The name on it said Ricky.
Luckily the plant has professional menders there to fix tears or stains, typically made by the customer, however, not the employee.
I started off in the stock room with Isela Castaneda and Shirley Wooten, a 20-year employee of UniFirst. On a weekly basis, they measure, sort and record hundreds of garments at the plant, among many other duties. I measured pants with Ms. Castaneda and tried to learn their process. Depending on the length, each pair of pants is given a color-coded label with the waist size written on it. Then they are sent to Ms. Wooten who enters them into a computer. She knows the number that each color corresponds to by heart as well at the multi-digit code that's associated with each style of pants. By the time, I could look up what length a purple label meant, she had already entered several pairs. I decided to move on.
I was told that it was hard work out on the main floor. I assumed that was because it was warmer out there with all the machines. What I didn't realize was that I'd be working with more numbers than in Calculus 101.
The process begins when the trucks, which run about 17 routes in Wayne County and 14 in Rocky Mount, bring in the dirty uniforms, towels and door mats. They are then hand-sorted and loaded into giant washing machines that are roughly the size of a living room. This is when I became envious of the washers. When the cycle is done, the washers hydraulically raise and dump the laundry out on a conveyer belt that runs across to the dryer, which essentially loads itself. Genius.
Once the clothes are damp, they are removed from the dryers. The pants are hung on a line that takes them through a tunnel that dries them wrinkle-free. The shirts are hung on torso-shaped mannequins. Once in place they are pressed and steamed by a contraption that looks like a shirt-shaped waffle iron.
Next the clothes are sorted before going to the shipping line. This is where all the numbers come into play. The clothes are sorted based on a 15-digit code on the tag that tells which of the 30 hooks it should be hung on, what route it should be sent to and what day the route is on.
I jumped in to "help" Sally Exum, a 14-year employee, as she sorted. To add to the confusion, the 30 hooks the clothes are hung on are not stationary, they are on clothes lines that zoom by you. So in a matter of seconds, I needed to find the code, decipher it and hang it on the appropriately numbered hook as it zooms by my head. After a few minutes, I thought I was getting into the groove, hanging shirts on the correct hook before it flew by. I found out, however, that what I thought was the correct hook and what Ms. Exum thought was the correct hook were very different things, as I saw her removing several of the shirts I had hung.
I left that station and ended the day at shipping with Bessie Hobbs, an 18-year employee.
"OK, to figure out the route it goes on, you have to look at the middle number of the first set of three numbers in the code," she said.
"I literally have no idea what you just said," I said.
I wrapped up the day feeling completely confused and still intrigued by the main floor, which had more things moving at once, zooming through the air that it was like the Willy Wonka Chocolate Factory of laundry. What was most interesting, though, was the number of long-time employees there were at UniFirst. Almost everyone I met that day had been there at least 15 years, not to mention the few all-stars like Ethel Battle, who recently celebrated her 50th year at UniFirst, and Chris Long who has been running a route for about 30 years.
"I like my job. I'm good at it and I enjoy it," Ms. Wooten said. "They were here for me when I needed them and they still are."
General manager John Walker summed it up simply when I asked about his employees.
"We take care of our people," he said.