Duke grant promotes jobs
By Phyllis Moore
Published in News on May 30, 2018 2:13 PM
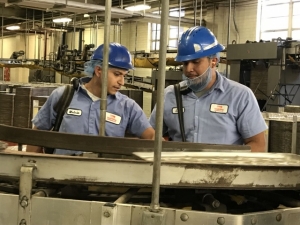
News-Argus/PHYLLIS MOORE
Melvin Martinez, left, and Luis Bartolon-Ortiz, work on a conveyer at Franklin Baking Company. The men are part of the apprenticeship program, affording employees the opportunity to take college courses while receiving on-the-job training.
Wayne Community College isn't just training people for jobs today -- it's preparing them for opportunities in the future.
Since being awarded a N.C. Community College Apprenticeship Grant for $200,000 -- one of two colleges in the state to receive it from Duke Energy -- efforts have escalated to formalize an apprenticeship program, said Craig Foucht, business and industry center executive director.
"We have been working with employees who support that," he said. "We have six businesses who want to support that and have gotten apprenticeships funded within their businesses."
In the past, apprenticeships in the county between industry and the college were a "work-based learning-type experience," Foucht said. The parameters consisted of employees taking classes at WCC and on-the-job training.
"Nobody's ever really formally tried to organize anything in Wayne County that has really tried to centralize it. It's been every employer just sort of working on their own," Foucht said. "Since we got awarded the Duke Energy grant, we've been helping employers to register apprenticeships."
That entails focusing on four components required with the state and federal government -- on-the-job learning, job-related education, a progressive wage scale and apprenticeship standards.
The standards tell what the job is and determines the length of time for the apprenticeship. Most opt for a two-year or four-year time frame.
The business determines what the employee has to do to be trained for the occupation.
The wage scale is a "journeyman's rate," which starts at no less than 50 percent of minimum wage and progressively climbs to 85 percent of that rate by the time the apprenticeship is completed.
And the last piece, where WCC comes in, is the job-related instruction, Foucht said.
"I try to tie it back to the college to a program that we have and it may not be a full associate's degree," he said. "It may be a certificate. It may be a diploma. It may be a mix of classes from different degree programs.
"Where we've been focusing mainly is in the maintenance side, because we knew that regardless of what manufacturers we were dealing with in the community, they still had to have somebody maintain the facility, maintain their equipment, so there was a lot of overlap."
Foucht gave an overview of the program to the WCC board of trustees at his recent meeting. He said several local businesses have signed on for the apprenticeship program.
Mt. Olive Pickle was the first one to back this and say they were going to help out, he said, with interest in the maintenance-based areas of mechatronics technician and machine operator.
"The next employer, which was actually the first employer to get their apprenticeship registered, was Franklin Baking," he said. "They've already got two people taking classes out here so there's two active apprentices right now on our campus. They're in the industrial system program.
"And this is one of the employers that actually chose an entire full associate's degree so when the students graduate from us and they finish their apprenticeship, they'll get multiple credentials."
The program there began around the first of the year, said human resources business partner Charles Brogden. The business had already been contemplating doing something along those lines as a way to build new talent, he said.
"This is really kind of providing incentive, especially for somebody that can't afford an education or wouldn't typically go get an education," he said.
"This is a way that they can start working and they're taking college classes."
So when Luis Bartolon-Ortiz and Melvin Martinez stepped up, and were already taking classes at the college, it was what Foucht called a "natural fit."
"These two guys were entry level in our maintenance department," Brogden said. "This was good also to catch them at the very beginning of the program.
"It worked out very well. They're go-getters."
Bartolon-Ortiz has worked at Franklin for about a year and a half, he said, and was interested in learning new things.
"First I was (studying) welding," he said. "(This has) given me an opportunity to take a shot at something I have never done. So far I"m enjoying it."
He said he especially likes the hands-on aspects of the on-the-job training.
That has always been the case for the 21-year-old.
"I like to take things apart and put them back together," he said. "As a little kid I would take my toys apart and put them back together."
Martinez, 25, has been employed at Franklin Baking for four years. Beyond the job skills, though, he has appreciated some of the intangible skills the apprenticeship experience provides.
"I'm learning a lot about how to be responsible and how to keep myself organized," he said.
Brogden praised the men's willingness to step up for the opportunity and accept the challenges it presents.
"I think it's important that they do want to better themselves, so we're very proud of them," he said.
Their job title now is Engineer I, which basically translates to working on the various machines at the company and keeping them running.
Others local industries partnering with WCC include Raymond Carolina Handling, Linamar and AP Exhaust, with SPX Transformer Solutions and Ryerson in the registration process.
Linamar is particularly unique, Foucht pointed out. The business is not even in Wayne County, but on the line between Wayne and Wilson counties.
"They chose the CNC operator (apprenticeship job)," he said. "This company has got a new contract, awarded by Honda. They will be adding 60 CNC operators.
"As soon as we got the registered apprenticeship done the next day the supervisor called me and said, 'So where's all my apprentices?'"
In response to that, a program is being created through the college's continuing education department, called a CNC boot camp that will be run for 10 weeks this summer.
The payoff from attending that could be a potentially big one, Foucht said.
"(Linamar) has guaranteed that every single person that successfully completes that, an interview," Foucht said. "Starting wage is $18.03 an hour. Their finishing wage is $24 an hour. So you've got somebody starting off, right off the street, after 10 weeks of training making over $36,000 a year and then within four years when they finish their competencies, literally making $50,000 a year."
Now that businesses in the community are finding out about the program, Foucht said interest among other employers is gaining momentum.
There is also discussion about youth apprenticeships, working with high school students and establishing free apprenticeships and waiving tuition for the college courses.
It doesn't stop there.
Foucht has his sights set on a federal grant that could fund even more options locally.
"There's $145 million that the U.S. Department of Labor has been tasked with spending to expand apprenticeships so really what they're looking at is different agencies, maybe state agencies, could even possibly be community colleges, we don't exactly know because the money has not been released" he said. "But the date that they got awarded the money to start spending was April 1, 2018 and it's supposed to be spent by June 30, 2019.
"I think we're strategically placed to be able to opefully go after some of this $145 million.